More progress today. Basically have to disassemble the mill to install the ball screws.
First I made a drill guide to shift the mount holes in the casting.
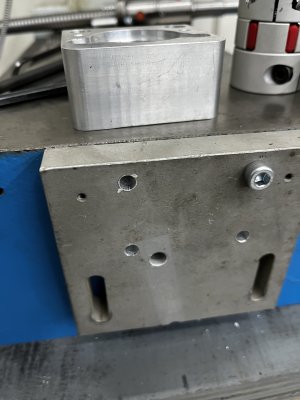
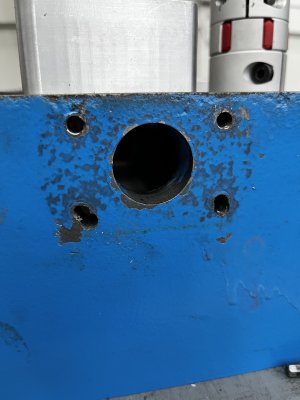
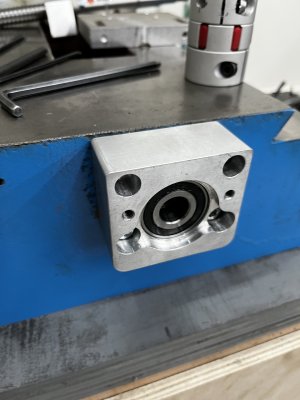
That worked out well so I turned my attention to taking the head and the column off so I could install the Y and Z axis ball screws.
I don’t have pics of this as it was very difficult to do.
There’s a gas strut in the column which was a complete pain in the rear to remove because unlike gas struts on a trunk for example, the strut couldn’t be popped off the ball. So I had lean the column back so I could unscrew the lower ball about 1/16 of a turn at a time for the length of the 1” stud.
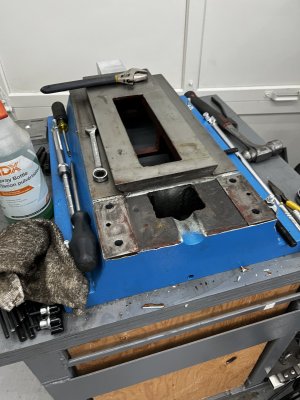
Once off I tried to slide the Y axis ball screw into place.
No dice as the base casting prevented the end from going all the way through the hole in the front of the base.
Break on the angle grinder and cut the opening an inch longer.
Dressed the new cut with a file and now the ball screw can slide into place.
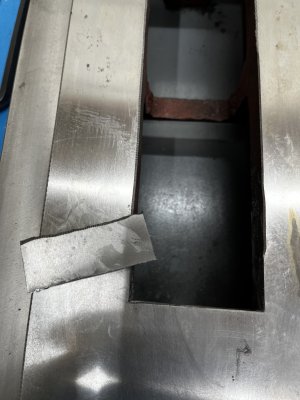
With the ball screw in place I put on the mount which contains two bearings for the driven end of the ball screw.
Mount fits perfectly on the shaft but the hole in the front of the casting isn’t large enough for the ball screw to drop down enough for the mount to match my up with my newly drill holes in the casting.
Off to Home Depot to buy a 1.25” hole saw to enlarge the hole.
With the hole enlarged it was easy to put everything together.
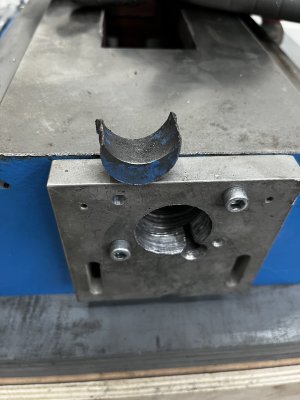
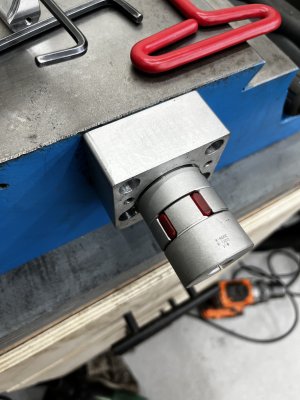