Gearhead88
Ultra Member
You are on the right track fixturing the cylinders like this . At one time I had considered using this approach .Here's a picture of what I was doing in the lathe. The slug in the 4 jaw is bored to just accept the sleeve were it protrudes from the bottom of the cylinder. The machined band on the outside is concentric so I can dial it in and I take a skim cut on the face each time I chuck it up so the cylinder registers on the base of the cylinder. I think the bore finish is good and no signs of chatter. I just don't know how much taper is OK.View attachment 28730
There are lots of examples of similar arrangements when you do a search , some good , some not so good .
Then there's the debate over should I fixture the cylinder in a static position and rotate the cutting tool ? or....... fixture the cylinder in a rotating setup like you have shown and use a large boring bar . Both will work , both require attention to setup and rigidity. There's lot's of interesting ideas out there.
I've used a few different dedicated machines to bore cylinders , having done that for some time , that's my preferred way .
Before I bought my own boring bar I mulled over ways I could possibly bore cylinder with the equipment I already had .
For what I do , I decided that it was better to just tool up with the right stuff and was fortunate to find a good deal on a Van Norman 944 boring bar which will take care of pretty much every bore I might have to do.
Some example of images I found .........
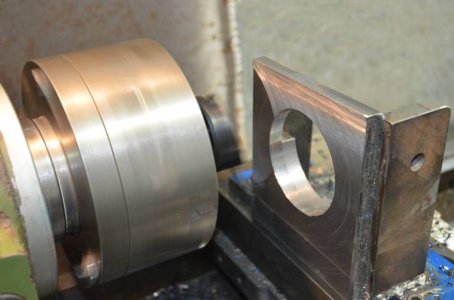
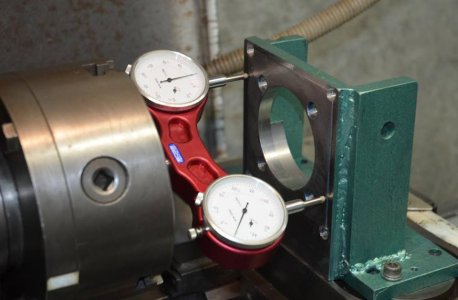
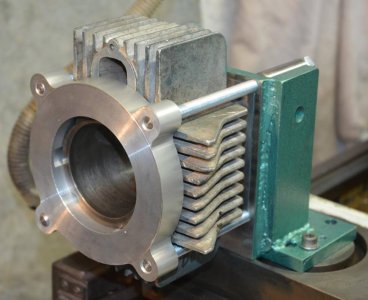
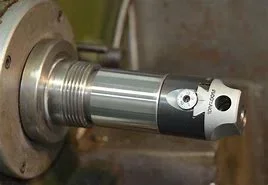
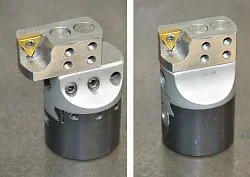
This one shows a cylinder being bored to remove a damaged liner and will be re- sleeved , the existing iron liner was cast in and has ribs to lock it into the cast aluminum , the sleeve portion of the liner is pretty much gone at this point , all that remains is the ribs that were cast into the iron liner.
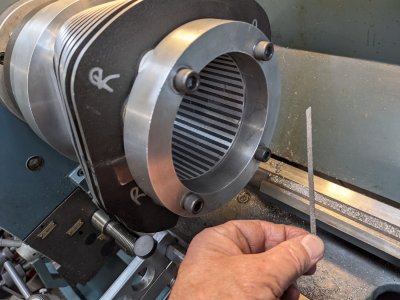
Last edited: