DPittman
Ultra Member
I had to take off about another 40 thousands of inch on the thickness of these little half moon shape spacers. I had done some hand filing but was getting crooked on them (and tired) and they needed to be fairly accurate.
I couldn't figure out any other way to hold them to skim off some material with the mill.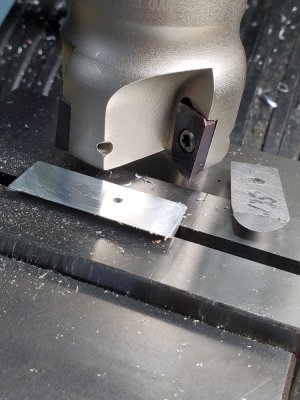
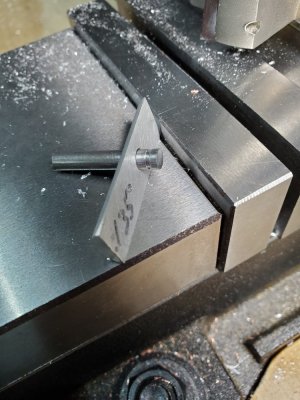
View attachment 11826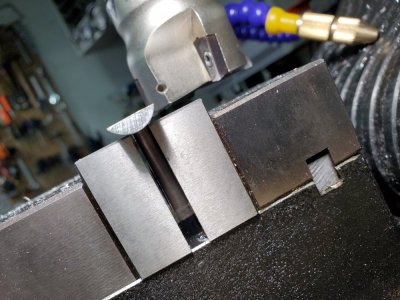
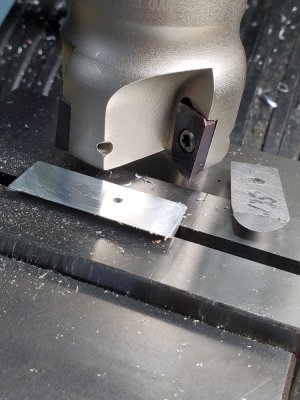
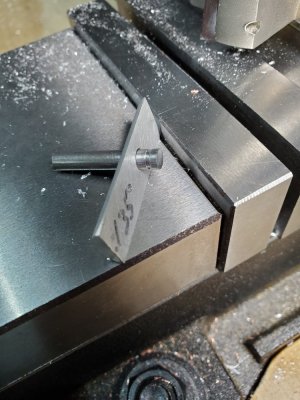
View attachment 11826
There was an existing 3/16 hole in the pieces already and I used loctite to hold a small piece of rod in the hole which I could then clamp onto with the vise.
Pictures will explain what I did better.
I knew it was risky but didn't figure I would ruin anything other than the part if it didn't work. It worked like a charm. I took only maximum 10 thou cut at a time cuz I was scared to bugger it all up. I think the reason it worked is because pretty much all the pressure was down ward across the face of the piece evenly.
The part is for a moving cocking mechanism on an air rifle.
I couldn't figure out any other way to hold them to skim off some material with the mill.
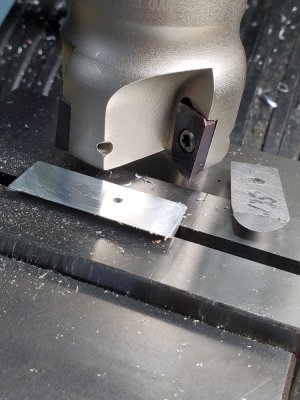
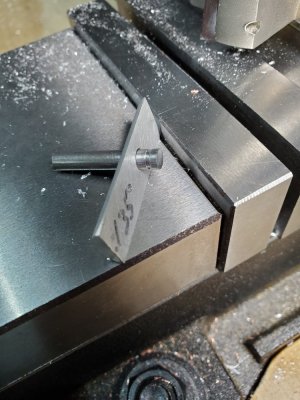
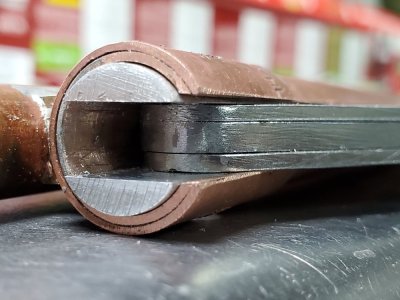
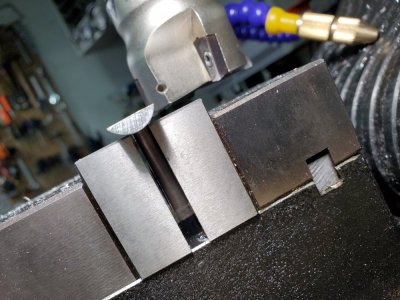
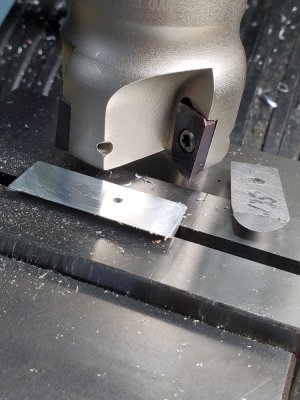
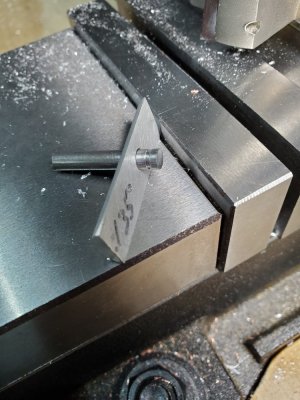
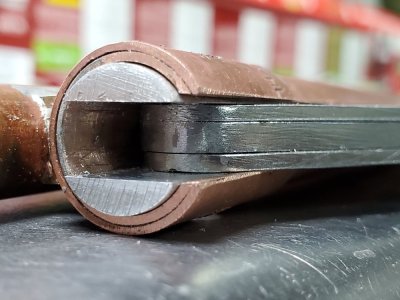
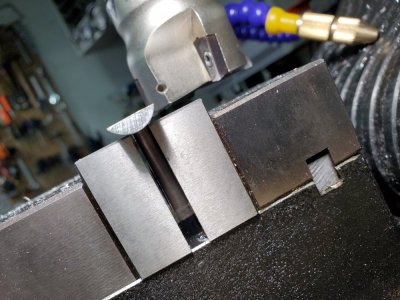
Pictures will explain what I did better.
I knew it was risky but didn't figure I would ruin anything other than the part if it didn't work. It worked like a charm. I took only maximum 10 thou cut at a time cuz I was scared to bugger it all up. I think the reason it worked is because pretty much all the pressure was down ward across the face of the piece evenly.
The part is for a moving cocking mechanism on an air rifle.