After being reminded of an excellent way to solve my "I never have the correct size handy" problem, I made my own set of BA and Imperial nut drivers. Thanks again for the inspiration to actually do this.
Now I just need to do some tests to see if milling a flat on each handle and engraving the socket size is a viable and worthwhile addition. (At least the BA nut drivers have a "band" cut in the handle to identify them as such.) It also remains to be seen if the "stands" are useful or a nuisance but it should help in finding the correct size in the interim. The storage stands are 3D printed but a block of lumber would have been as useful. What good are all the toys if we don't play with them though?
The pile of hex ended pieces are the dies made to form (i.e., forge) the sockets on ...
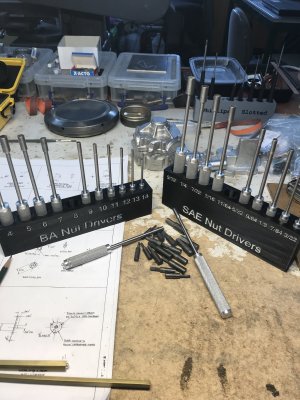
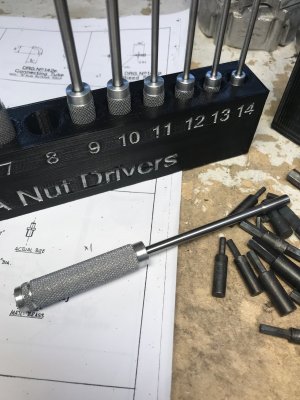
Now I just need to do some tests to see if milling a flat on each handle and engraving the socket size is a viable and worthwhile addition. (At least the BA nut drivers have a "band" cut in the handle to identify them as such.) It also remains to be seen if the "stands" are useful or a nuisance but it should help in finding the correct size in the interim. The storage stands are 3D printed but a block of lumber would have been as useful. What good are all the toys if we don't play with them though?
The pile of hex ended pieces are the dies made to form (i.e., forge) the sockets on ...
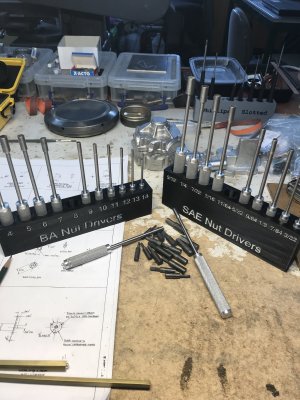
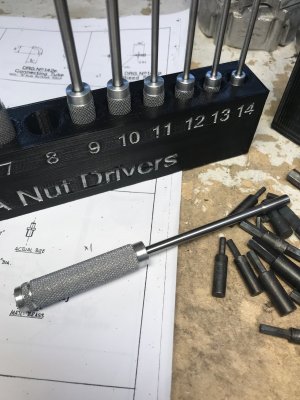