It all started with the rotary broach project....
Took a “ no name “ live center apart to see how it worked and see if I could adapt it for a rotary broach. It was also pretty crusty when turning the spindle by hand. It needed cleaning and possibly new bearings... Well, I have since refurbished three LCs: the “No Name” DM 313, a Hardinge HDC and a Skoda. The Hardinge was part of another tool purchase - the spindle felt like there was sand in it. The Skoda came with my SM 1340 and I knew it had issues.
All centers are working like new after a thorough cleaning and lube. Each center had different innerts which I thought might be of interest.
Here is a pic of the DM 313. It has a common ball bearing followed by a thrust bearing and a little needle roller bearing on the tail end.
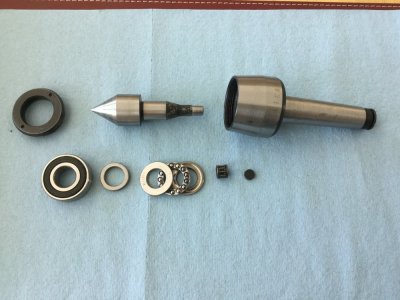
The Hardinge has two precision angular contact ball bearings, ACBB, back to back separated by outer and inner race spacers. This whole assembly pushes against a thin, ground washer which sits on a raised boss in the back of the housing and presumably flexes under thrust loads. Me thinks that that is to compensate for the thermal expansion of the workpiece. Clever.
Here is the stack-up
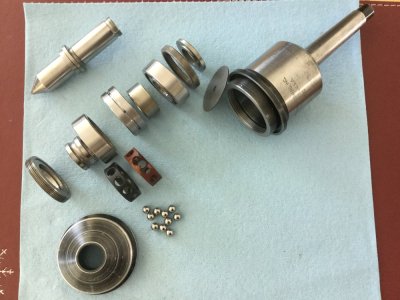
Here you can see the raised boss at the bottom of the housing
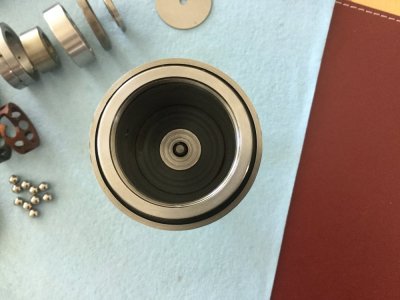
And with the ground flex washer sitting on top of it. The pin locates the washer.
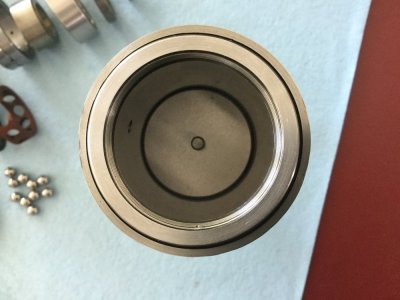
The spindle with both bearings, spacers and bearing retainer before they are inserted in the housing

All together
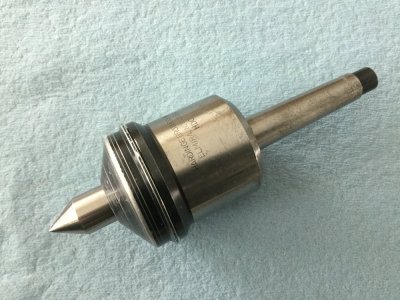
Yes, I did break the cage of the front ACBB on disassembly. So I made one out of Delrin. You can see the busted one (reddish brown colour) and the new (black colour) Delrin one in the stack-up pic above. The reason for the “sand in the bearings” feel was dried out grease. So I switched the lubrication to lost oil lube. You can see the newly machined radial groove and the oil holes in the outer bearing race spacer ring. I also located a little oil hole with a plug screw in the housing.
Lastly, here is the Skoda. It consists of a needle roller bearing with a split conical outer race that gets pushed into a tapered seat in the front of the housing. Then there is a conventional thrust bearing and at the very tiny tail end a small ball bearing.
Here is the stack-up
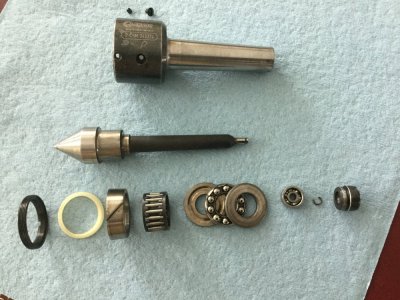
The white ring acts as a dust shield. This LC is set up from the factory as a lost oil lube system. Note the little oil port and screw in the housing.
Here is a view of the tapered surface into which the bearing cone mates.
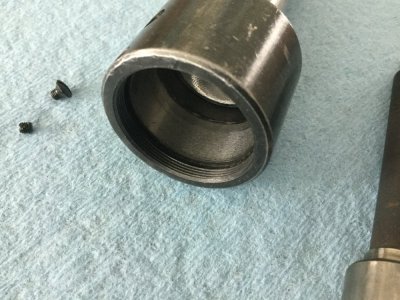
There are no markings on the split cone. My guess is that Skoda made that in house. Note how the slit is at an angle (see prev. pic) so that the rollers can glide across it freely. Again, clever as one can take up any play in the bearing by pushing the cone deeper into the housing, thus compressing it, with the front retaining ring.
I’m sure there are many other LC designs out there. These are the three I came across so far...
Took a “ no name “ live center apart to see how it worked and see if I could adapt it for a rotary broach. It was also pretty crusty when turning the spindle by hand. It needed cleaning and possibly new bearings... Well, I have since refurbished three LCs: the “No Name” DM 313, a Hardinge HDC and a Skoda. The Hardinge was part of another tool purchase - the spindle felt like there was sand in it. The Skoda came with my SM 1340 and I knew it had issues.
All centers are working like new after a thorough cleaning and lube. Each center had different innerts which I thought might be of interest.
Here is a pic of the DM 313. It has a common ball bearing followed by a thrust bearing and a little needle roller bearing on the tail end.
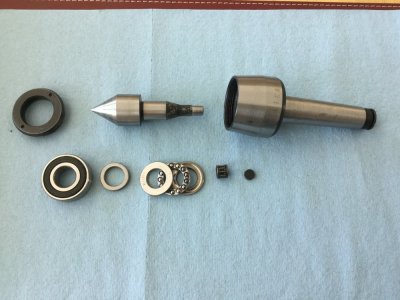
The Hardinge has two precision angular contact ball bearings, ACBB, back to back separated by outer and inner race spacers. This whole assembly pushes against a thin, ground washer which sits on a raised boss in the back of the housing and presumably flexes under thrust loads. Me thinks that that is to compensate for the thermal expansion of the workpiece. Clever.
Here is the stack-up
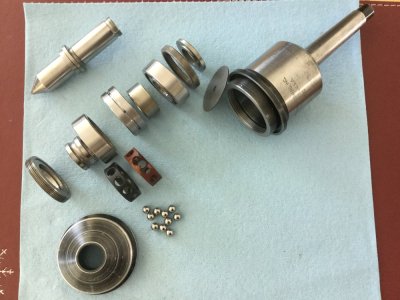
Here you can see the raised boss at the bottom of the housing
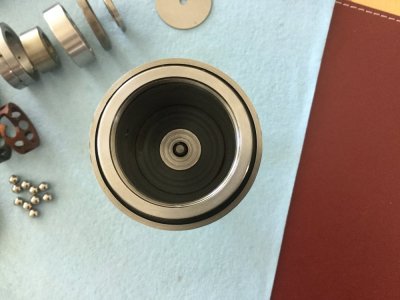
And with the ground flex washer sitting on top of it. The pin locates the washer.
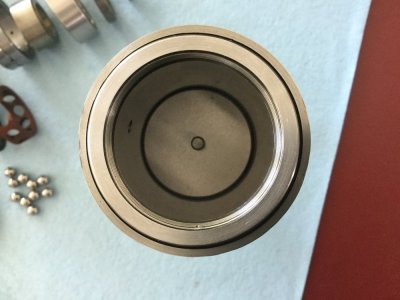
The spindle with both bearings, spacers and bearing retainer before they are inserted in the housing

All together
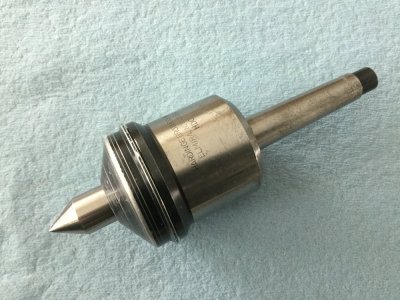
Yes, I did break the cage of the front ACBB on disassembly. So I made one out of Delrin. You can see the busted one (reddish brown colour) and the new (black colour) Delrin one in the stack-up pic above. The reason for the “sand in the bearings” feel was dried out grease. So I switched the lubrication to lost oil lube. You can see the newly machined radial groove and the oil holes in the outer bearing race spacer ring. I also located a little oil hole with a plug screw in the housing.
Lastly, here is the Skoda. It consists of a needle roller bearing with a split conical outer race that gets pushed into a tapered seat in the front of the housing. Then there is a conventional thrust bearing and at the very tiny tail end a small ball bearing.
Here is the stack-up
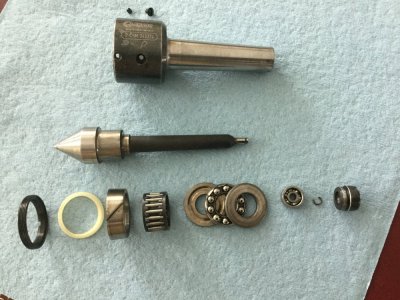
The white ring acts as a dust shield. This LC is set up from the factory as a lost oil lube system. Note the little oil port and screw in the housing.
Here is a view of the tapered surface into which the bearing cone mates.
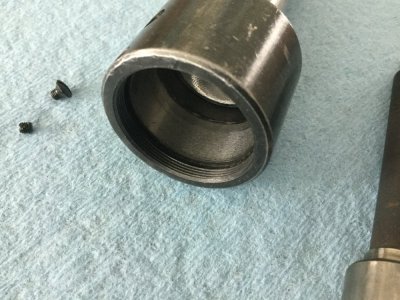
There are no markings on the split cone. My guess is that Skoda made that in house. Note how the slit is at an angle (see prev. pic) so that the rollers can glide across it freely. Again, clever as one can take up any play in the bearing by pushing the cone deeper into the housing, thus compressing it, with the front retaining ring.
I’m sure there are many other LC designs out there. These are the three I came across so far...
Last edited: