Tmate
Well-Known Member
A lack of distance between the spindle and table appears to be a universal issue for owners of these popular import mills. I think I may have come up with a relatively easy to fabricate riser block to fix the problem.
McMaster-Carr carries a 6" dia. pipe flange (Pt.#68905K389) that is almost made to order for this riser block project. They are 6" in diameter, 3/4" thick, with a 3.10" x 1/4" flange on one side. They come with four 3/4" bolt holes, two of which will be used for dowel pins for alignment purposes. A third will be used for one of the hold-down bolts. Two 1/2" diameter holes will be drilled in each plate for the other two hold down bolts. Additional detail is included in the second image below.
They cost approximately $26.00 each, and with slight modification, will stack pancake style to whatever height you desire. The machine work necessary is:
Drill two 1/2" holes in each plate
Mill or face the flange off all but one plate
Bore the existing center hole in one plate to 3.10"
Cut to length two 3/4" dowel pins (drill rod or CR round)
I'm waiting for warm day to install it. There may be some minor dimension differences in these mills depending on name brand. It's a good idea to check dimensions on yours before going too far.
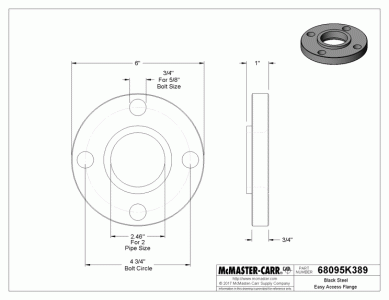
McMaster-Carr carries a 6" dia. pipe flange (Pt.#68905K389) that is almost made to order for this riser block project. They are 6" in diameter, 3/4" thick, with a 3.10" x 1/4" flange on one side. They come with four 3/4" bolt holes, two of which will be used for dowel pins for alignment purposes. A third will be used for one of the hold-down bolts. Two 1/2" diameter holes will be drilled in each plate for the other two hold down bolts. Additional detail is included in the second image below.
They cost approximately $26.00 each, and with slight modification, will stack pancake style to whatever height you desire. The machine work necessary is:
Drill two 1/2" holes in each plate
Mill or face the flange off all but one plate
Bore the existing center hole in one plate to 3.10"
Cut to length two 3/4" dowel pins (drill rod or CR round)
I'm waiting for warm day to install it. There may be some minor dimension differences in these mills depending on name brand. It's a good idea to check dimensions on yours before going too far.
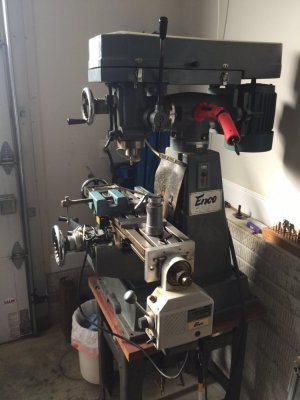
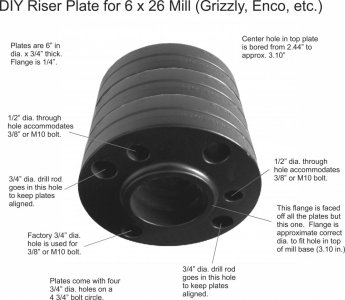
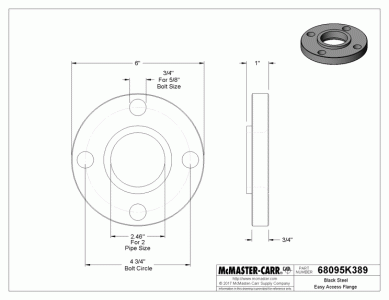