140mower
Don
A couple years ago I found an old South Bend for sale a couple hours away from home. It's a 1929 series O 13" with single tumbler gear box.
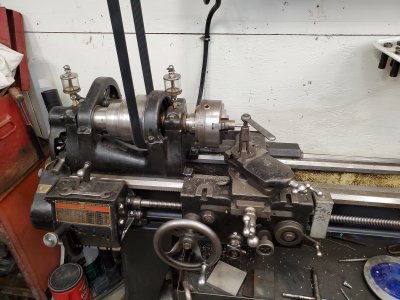
It came with three and four jaw chucks, two fixed steadies traveling steady, face plate, dog driver and a few extras. All in all it shows very little wear for its age, and is a welcome improvement to my little shop.
I plan on making this a multi post event that brings it to life, including the making of a gear cutting attachment for the shaper, and overcoming my fear of electricity and wiring up my phase converter after the single phase motor on the shaper went up in smoke midway through.....
Will take a while to piece it together, but I will try to not drag it out as long as it took to do it.
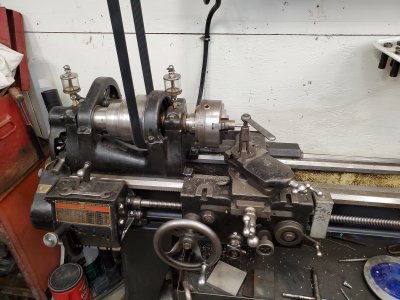
It came with three and four jaw chucks, two fixed steadies traveling steady, face plate, dog driver and a few extras. All in all it shows very little wear for its age, and is a welcome improvement to my little shop.
I plan on making this a multi post event that brings it to life, including the making of a gear cutting attachment for the shaper, and overcoming my fear of electricity and wiring up my phase converter after the single phase motor on the shaper went up in smoke midway through.....
Will take a while to piece it together, but I will try to not drag it out as long as it took to do it.